Posted 07/11/16
My last post on this subject described my successful effort to mount my Mongoose IMU on Wall-E2, my wall-following robot. I showed that the IMU, mounted on an 11cm wood stalk on Wall-E2’s top deck, when calibrated using my Magnetometer Calibration tool, provided reasonably accurate and consistent magnetic heading measurements.
This post attempts to extend these results by replacing the long wooden stalk with a more compact plastic mounting bracket (actually my original IMU mounting bracket) as shown below
In an effort to determine what, if any, effect the stalk mounting had on IMU calibration, I decided to acquire and plot calibrated (as opposed to raw) magnetometer data using my mag cal tool, and compare it to the results of the calibration performed on the stalk-mounted configuration. Since I don’t currently save the ‘calibrated’ point-cloud (there’s no need, as all it does is show how well (or poorly) the raw mag data point cloud is transformed using the generated calibration matrix/center offset values), I first had to import the saved raw data from the stalk-mounted configuration and then regenerate the calibration values (and the resultant ‘calibrated’ point cloud). Once this was done, then I can capture the new calibrated (i.e. calibrated using the previous stalk-mounted calibration values) but now in the lower mounting position. If the stalk mounting had no additional isolation effect, the two point clouds should look identical. If the stalk mounting did have some effect, then the two clouds should look different.
I started by launching the mag cal tool and importing the raw mag data captured 07/06/16. Then I computed the calibration factors and the resulting ‘calibrated’ point cloud, as shown in the following screenshot.
As can be seen from the image, the data calibrated quite well, starting with a visibly offset point cloud with an average radius of about 450, and ending with a well-centered and symmetric point cloud with a radius close to 1.
Next, I captured a set of data from the bracket-mounted IMU, using the calibration values from the 6 July stalk-mounted config (this required a bit of reprogramming to pare back the reporting from Wall-E2 to just the magnetometer 3-axis data). The data was captured by manually rotating Wall-E2 about all 3 axes in a way that produced a well-populated ‘point cloud’ in the mag cal tool app. During this run, Wall-E2 had power applied, and all motor drives enabled.
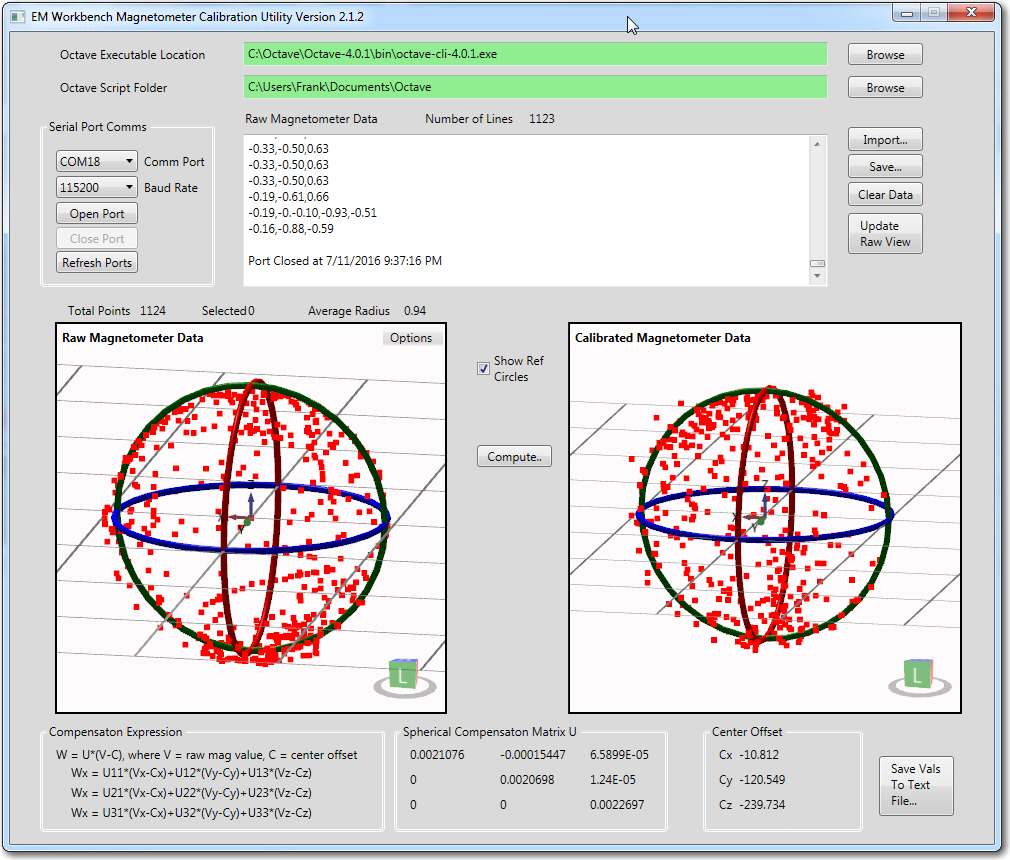
Bracket-mounted IMU calibrated magnetometer data vs 06 July stalk-mounted computed calibration data, with Wall-E2 power on and motors running.
From the above screenshot it is quite clear that the stalk and bracket mounting configurations are essentially identical in terms of their calibrated performance. This means I could, if I so chose, simply use the stalk-mounted calibration values and party on. Moreover, if I do chose to re-calibrate, I wouldn’t expect to see much change in the calibration values.
Here’s a short movie showing the calibration process:
After noting that the ‘stalk’ calibration values appeared to be reasonably valid for the bracket-mounted configuration, I re-ran the heading error tests on my bench-top heading range, with the following results:
For comparison, here is the ‘stalk’ heading error chart
And the original problem measurement from back in March with the IMU mounted on the first deck at the front of the robot:
From the above, it is kind of hard for me to believe that this much error could possibly be corrected just via the calibration matrix and center offset adjustments, so I suspect the current performance depends as much on moving the IMU from directly over the front motors to the 2nd deck (a minimum of 10cm from the rear motors, and about 15 from the front ones) as it does on the calibration values. I could verify this by re-mounting the IMU on the front and seeing if I could calibrate out the errors, but I’d rather let sleeping dogs lie at this point ;-).
Frank