Just as I was contemplating the dive into 3D printing, a friend came to me with an interesting problem. Ray is an avid bicycler, and he has a number of auxiliary gadgets attached to his bicycle. One of these gadgets is an auxiliary instrument holder that clamps onto the horizontal tube from the vertical fork tube to the handlebars, and provides its own small ‘handlebar’ for more instruments, as shown in the following picture
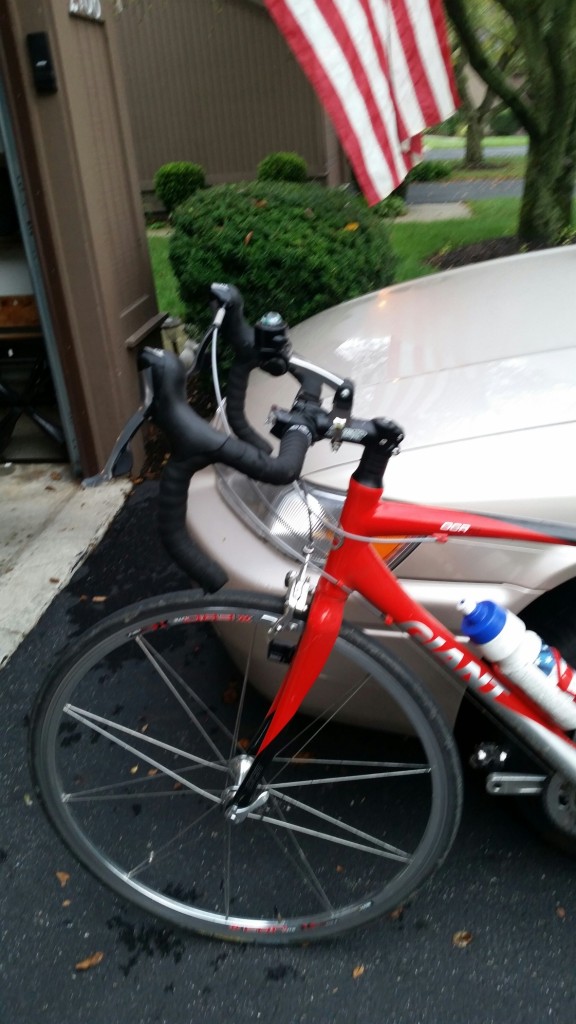
Side view showing aux instrument bar holder clamped to horizontal fork tube
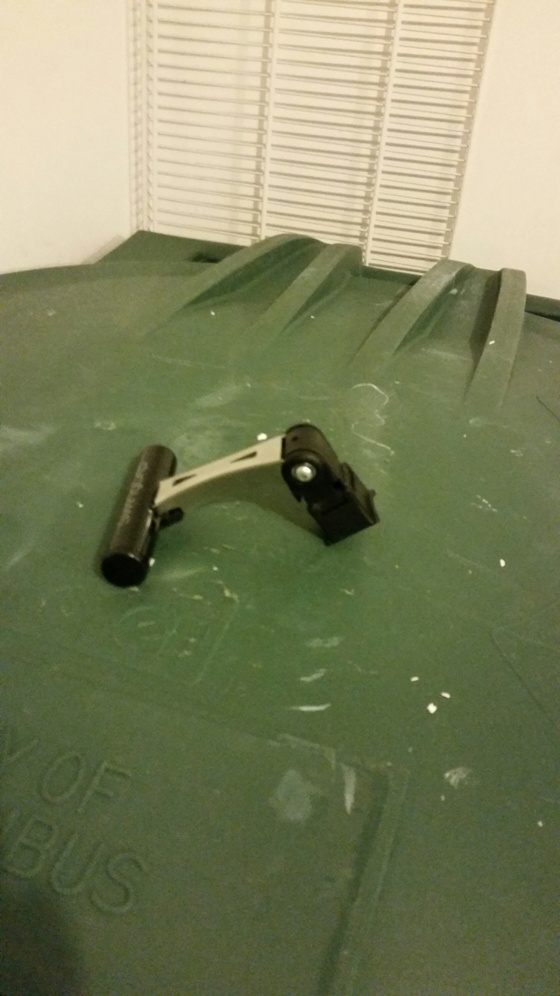
Side view of aux instrument holder
Unfortunately, after a short time the strap that holds the instrument holder to the bicycle broke, rendering the whole thing useless. The first time he thought it was maybe it was just a random manufacturing defect, but after going through several that all exhibited the same failure mode, he basically gave up on that model. When I mentioned that I might be able to help out with my brand-new PrintrBot 3D printer, he brought me the parts.
When Ray brought the broken clamp in, it quickly became obvious what the problem was, and why it was breaking so quickly. the system uses a metal band that is drawn down into a cavity by an adjustment screw, and this action requires the clamp band to make a right-angle turn right at the nut on the screw. The band metal is thin steel, and quickly develops fatigue cracks right at the bend.
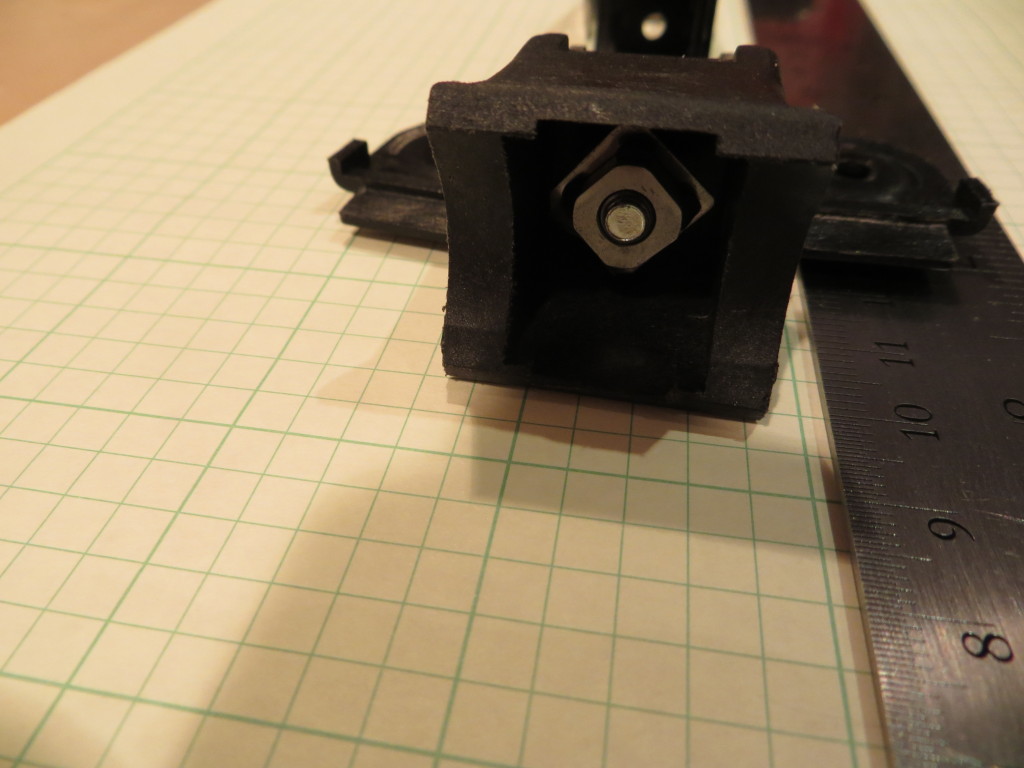
Mounting clamp interior view showing the capture nut
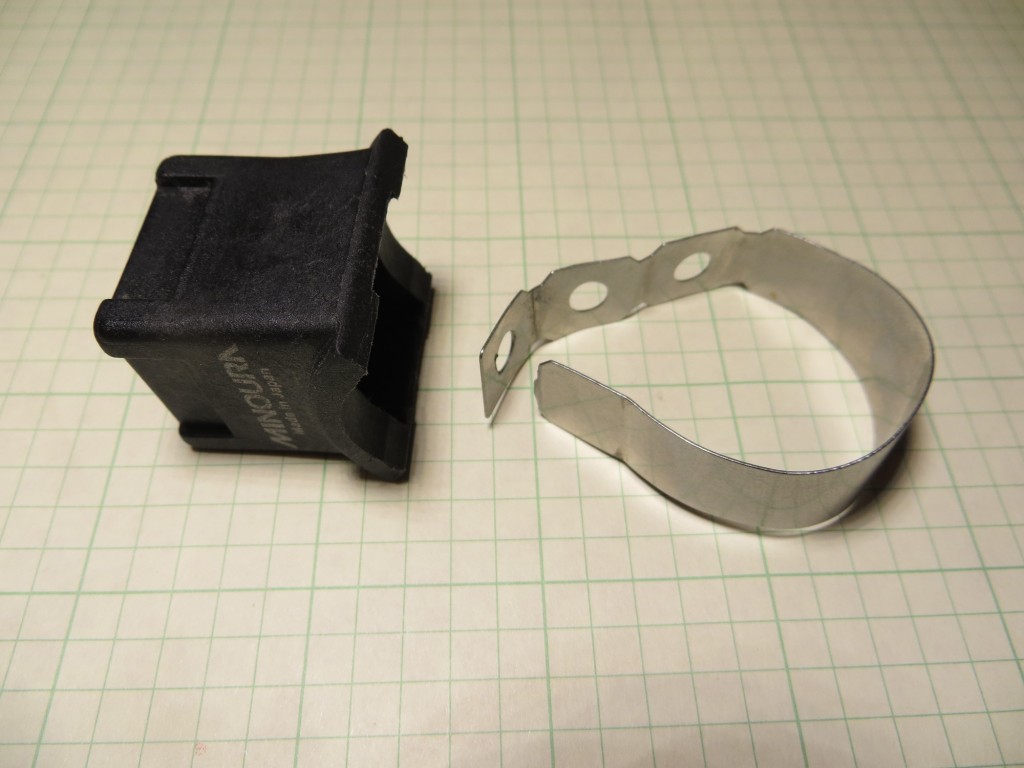
Mounting clamp and steel strap. Note the break occurs right at the right-angle bend
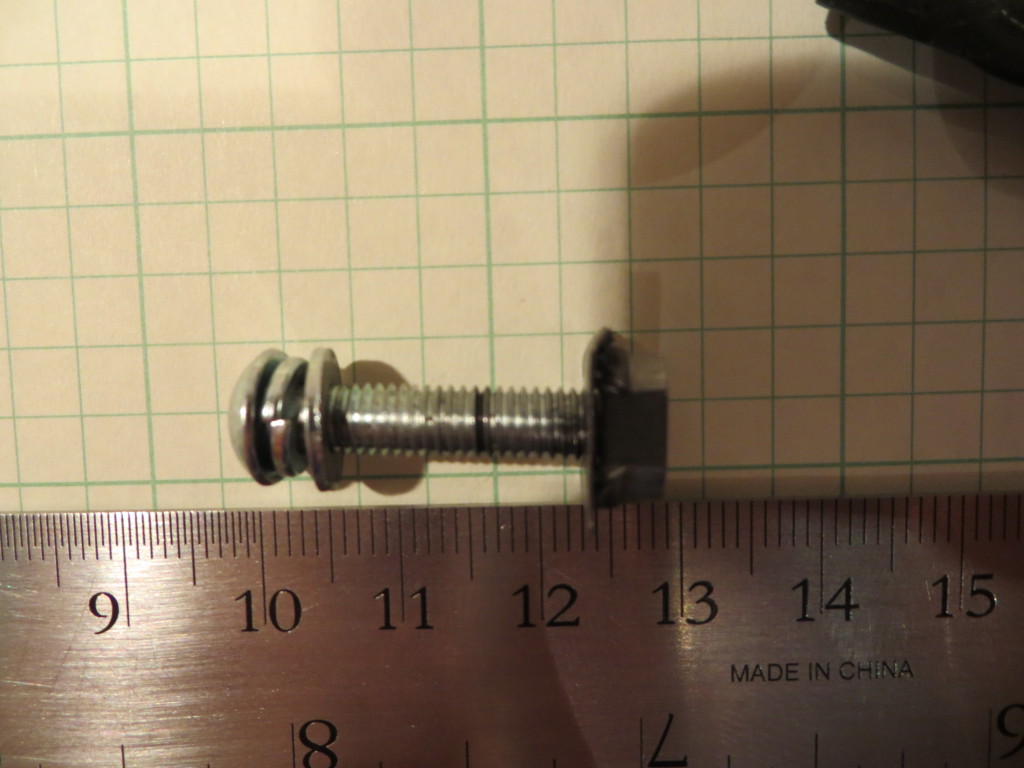
Capture bolt/nut. Notice the strap residue still on the nut
After some thought, I decided that the solution was not to try and reproduce the system exactly, but to redesign the clamping system to use a standard pipe clamp instead of the steel strap. The trick would be to ‘cut’ a slot through the body of the plastic clamp in such a way as to still allow the mounting bolt to attach the clamp to the rest of the system, while still leaving enough thickness to prevent the pipe clamp from breaking through the plastic part under load.
After going through a number of revisions and downright mistakes, I finally got a product that worked. One of the mistakes I made was trying to create the part without a decent set of calipers for precision measurements, resulting in a part that was about 10% undersized in one dimension, and about 10% oversized in the other. I remedied this problem by getting a very nice Fowler digital caliper from McMaster-Carr. Another minor problem was that the capture screw was too long, and interfered with the pipe clamp band. I solved this problem by simply cutting down the bolt a bit with a hacksaw, as the extra length was no longer needed. Also, as this was my first real 3D printing project, the print quality left something to be desired. Since this project, I have figured out how to get much higher quality prints.
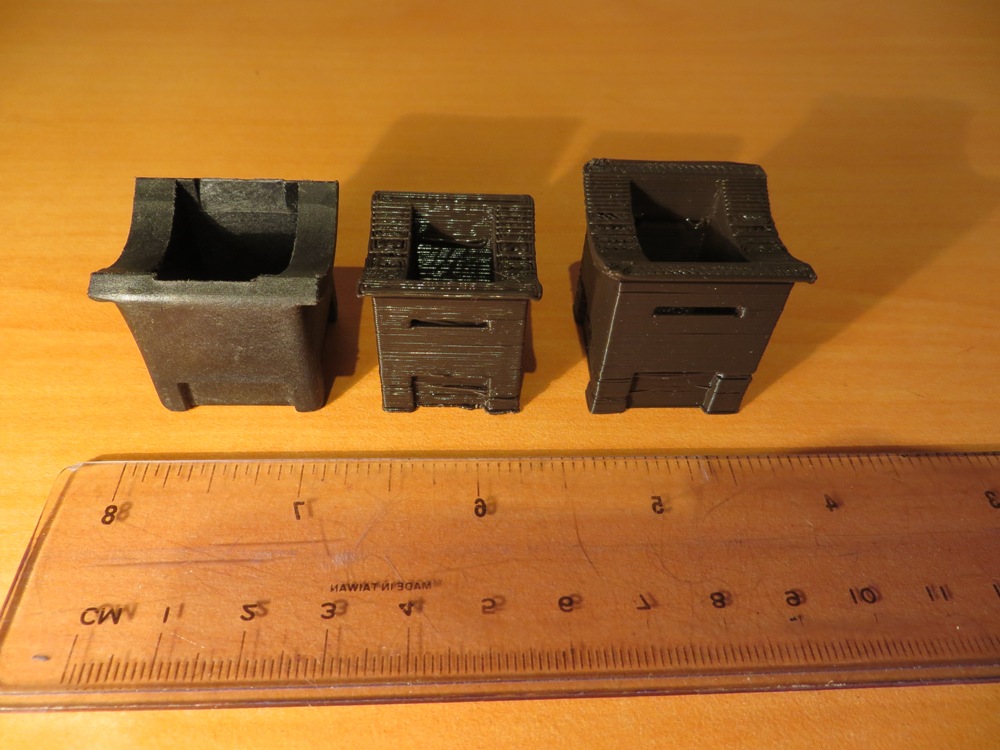
Original clamp on left, mis-sized version in center, final version on left. Note slots for pipe clamp band
After action reporting: Ray reported that the new clamp worked perfectly on his bike, and seems to be holding up very well.
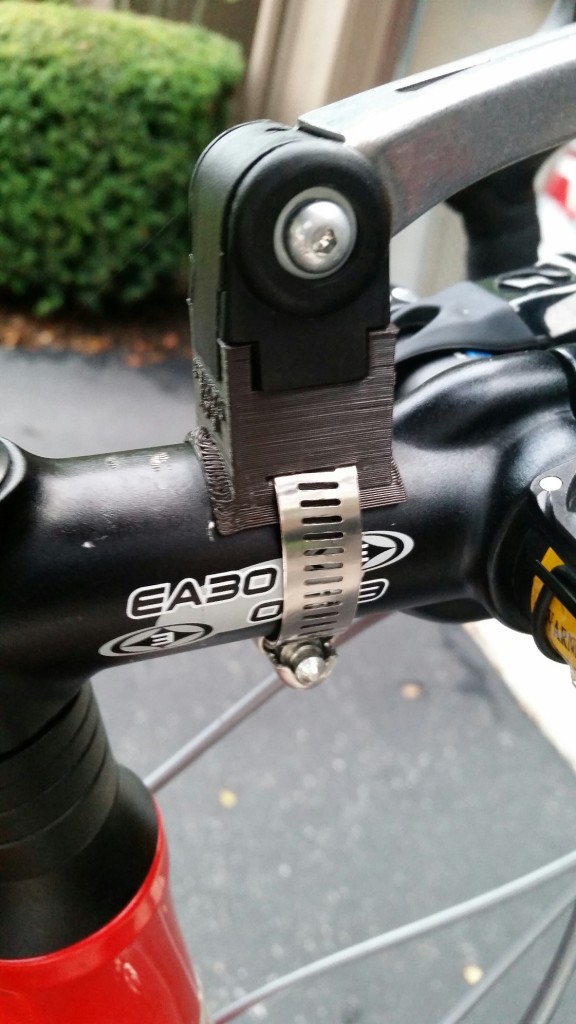